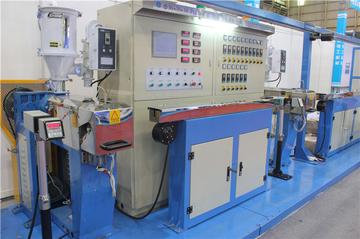
在挤压系统里,重点谈谈机头和模具的问题,因为机头的压力和模具的配比直接决定了电缆的质量。机头由合金钢内套和碳素钢外套构成,机头内装有成型模具。机头的作用是将旋转运动的塑料熔体转变为平行直线运动,均匀平稳的导入模套中,并赋予塑料以必要的成型压力。塑料在机筒内塑化压实,经多孔滤板沿一定的流道通过机头脖颈流入机头成型模具,模芯模套适当配合,形成截面不断减小的环形空隙,使塑料熔体在芯线的周围形成连续密实的管状包覆层。为保证机头内塑料流道合理,消除积存塑料的死角,往往安置有分流套筒,为消除塑料挤出时压力波动,也有设置均压环的。机头上还装有模具校正和调整的装置,便于调整和校正模芯和模套的同心度。
挤塑质量常见问题分析及解决方法
|
|
|
|
|
|
|
|
|
|
|
|
|
|
|
|
|
|
|
|
|
|
|
|
|
|
|
|
|
|
|
|
|
|
|
|
|
|
|
|
|
|
|
|
|
|
|
|
|
|
|
|
|
|
|
|
|